This summer, I had the pleasure to work at a startup, Figur8, which seeks to digitize 3D body movement easily for everyone. The sensor is encased in a rectangular shape, and one of the projects I worked on was to develop a new hardware attachment that could place the sensor on different parts of the body. A hardware attachment needed to be made that securely holds the sensor to one's arm, shoe, wrist, and hip.
This summer, I had the pleasure to work at a startup, Figur8, which seeks to digitize 3D body movement easily for everyone. The sensor is encased in a rectangular shape, and one of the projects I worked on was to develop a new hardware attachment that could place the sensor on different parts of the body. A hardware attachment needed to be made that securely holds the sensor to one's arm, shoe, wrist, and hip.
This summer, I had the pleasure to work at a startup, Figur8, which seeks to digitize 3D body movement easily for everyone. The sensor is encased in a rectangular shape, and one of the projects I worked on was to develop a new hardware attachment that could place the sensor on different parts of the body. A hardware attachment needed to be made that securely holds the sensor to one's arm, shoe, wrist, and hip.
This summer, I had the pleasure to work at a startup, Figur8, which seeks to digitize 3D body movement easily for everyone. The sensor is encased in a rectangular shape, and one of the projects I worked on was to develop a new hardware attachment that could place the sensor on different parts of the body. A hardware attachment needed to be made that securely holds the sensor to one's arm, shoe, wrist, and hip.
This summer, I had the pleasure to work at a startup, Figur8, which seeks to digitize 3D body movement easily for everyone. The sensor is encased in a rectangular shape, and one of the projects I worked on was to develop a new hardware attachment that could place the sensor on different parts of the body. A hardware attachment needed to be made that securely holds the sensor to one's arm, shoe, wrist, and hip.

Dynamic Dimensional Structure
Building Interactive Large-Scale Structures.
Overview
Project
Class
Team
Period
Skills
Materials
Design: Technique & Technology (MIT Course #: 4.101)
Team Lead (Team of 4)
Feb - May 2017
Dynamic Dimensional Structure
Human-Object Interaction, Back-of-the-Napkin Engineering Calculations, Translating Small Scale to Large-Scale Prototyping, Design and development physical structures that explore and exploit relationships between form, material, and behavior, Building large-scale structures and testing the limits of their structural, behavioral, or formal characteristics
Fiberglass Rods, Weather Balloons, Kite String, Bricks, Helium, Carabiners
Objective
Dynamic Dimensional Structure aims to create a dynamically changeable structure that begins as a 2D form and is able to expand into various 3D forms based on the strategic placement of connections and balloons. In a team of 4, we were able to achieve a dynamic, modular structure that transformed from a 6 ft tall hexagon prism to a 18 ft tall triangle prism.
Fiberglass robs, kite string, and carabiners were used in the creation of this project. Kite string was looped through the fiberglass rods in such a way to make a triangular prism shape. Six of these were created in order to form the shapes of both the hexagon and tower. No rods were removed or added in the transition from each form. Carabiners allowed the prisms to be rotated and aided the fluid transition from a 2D shape to a hexagon to a tower.
Materials
During the brainstorming phase, our group was particularly interesting in how gravity can be utilized to create interesting structures. The diagram to below accurately explains our thought process on how a structure could dynamically change depending on what nodes are being held stationary.
Approach

Prototyping
To quickly prototype our ideas, we used straws and strings to experiment with different connections and shapes to narrow down what creative and interesting structures our team wanted to achieve.

Once the final design for the structure was finalized, we began to assemble the structure on a much bigger scale: with 6 ft fiberglass rods. In order to shift around different modules of the structure. Each module was based off of a triangular prism. We utilized carabiners to easily deteach and attach the modules to different areas. Calculations were also made to estimate how much helium would be required to lift all the carbon-fiber tubes.
Finalized
Design

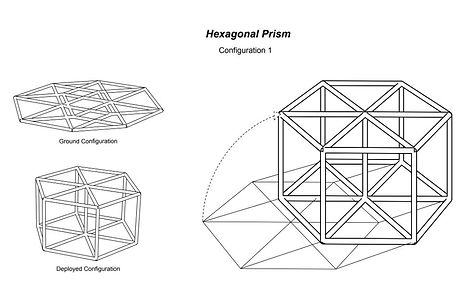
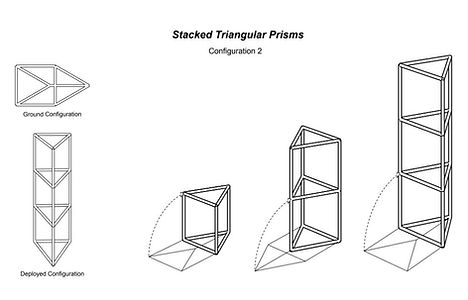
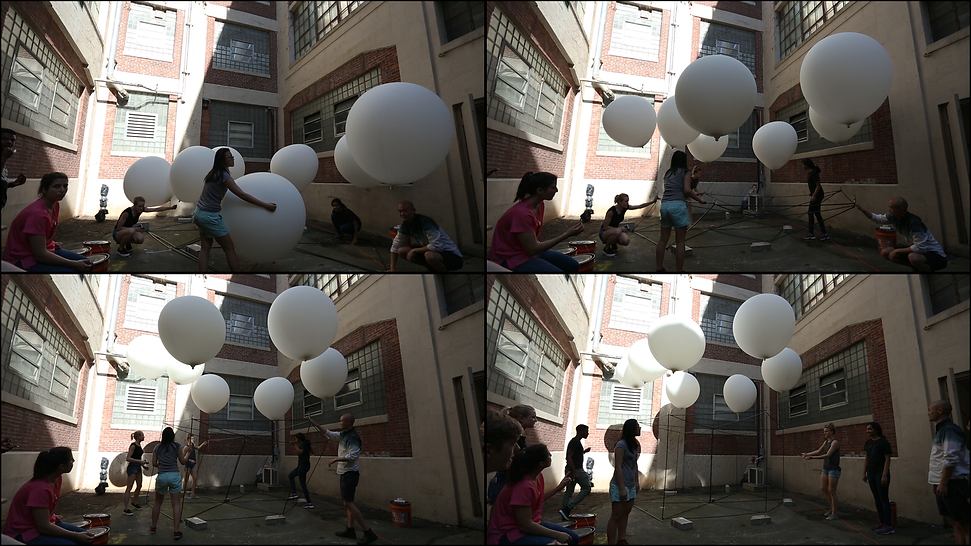
Above is a frame-by-frame process of the hexagon configuration being deployed.

Above is a frame-by-frame process of the tower configuration being deployed.
Videos
Video of hexagon being deployed
Video of tower being deployed